Unveiling the Production Process of Heated Apparel: From Design to Finished Product
Heated apparel has become a game-changer in the world of clothing, providing warmth and comfort in a variety of environments, from outdoor adventures to everyday wear. This blog delves into the detailed production process of heated apparel, from the initial design phase to the final product. We will explore each critical step, ensuring a comprehensive understanding of what goes into creating these innovative garments.

1. Identifying the Use Case
The journey of producing heated apparel begins with identifying the specific use case. Understanding the target market and customer needs is crucial to determining the product’s functionality and design.
- Analyzing Needs: The first step is to gather information about the intended use of the product. Is it for outdoor sports, industrial workwear, or everyday warmth? Each scenario has unique requirements.
- Defining Requirements: Once the use case is clear, the specific requirements such as temperature range, environmental conditions, and activity levels are defined to guide the design and material selection.
2. Designing the Garment
Designing the garment involves balancing aesthetics with functionality. With over 11 years of experience in the heated apparel industry, we leverage our deep understanding of customer needs and market trends to provide the most suitable and innovative designs.
- Fashion Trends: Keeping up with the latest fashion trends is essential to create appealing designs. Trend analysis helps in making informed decisions about colors, patterns, and styles.
- Functional Design: Integrating the heating elements without compromising on style is a challenge. Our extensive experience enables us to design layouts that ensure the heating elements are strategically placed for maximum comfort and efficiency.
- Initial Sketches: Creating preliminary sketches to visualize the garment’s appearance and functionality. These sketches undergo internal reviews and iterations.
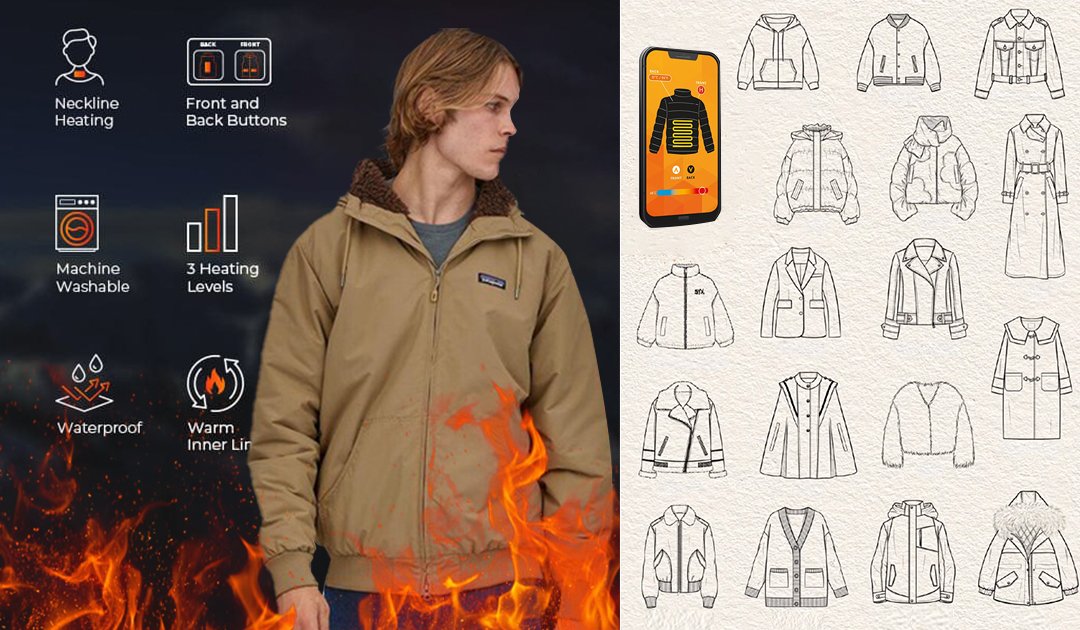
3. Selecting the Fabric
Choosing the right fabric is crucial for the performance and comfort of the heated apparel. Our expertise in material science allows us to recommend the best fabrics that meet the specific needs of each project.
- Fabric Characteristics: The fabric must match the product’s intended use. For example, outdoor sports may require waterproof and windproof materials, while everyday wear might prioritize softness and breathability.
- Material Selection: Common fabrics include polyester, nylon, and cotton. Each material is evaluated for its suitability based on the defined requirements and our in-depth industry knowledge.
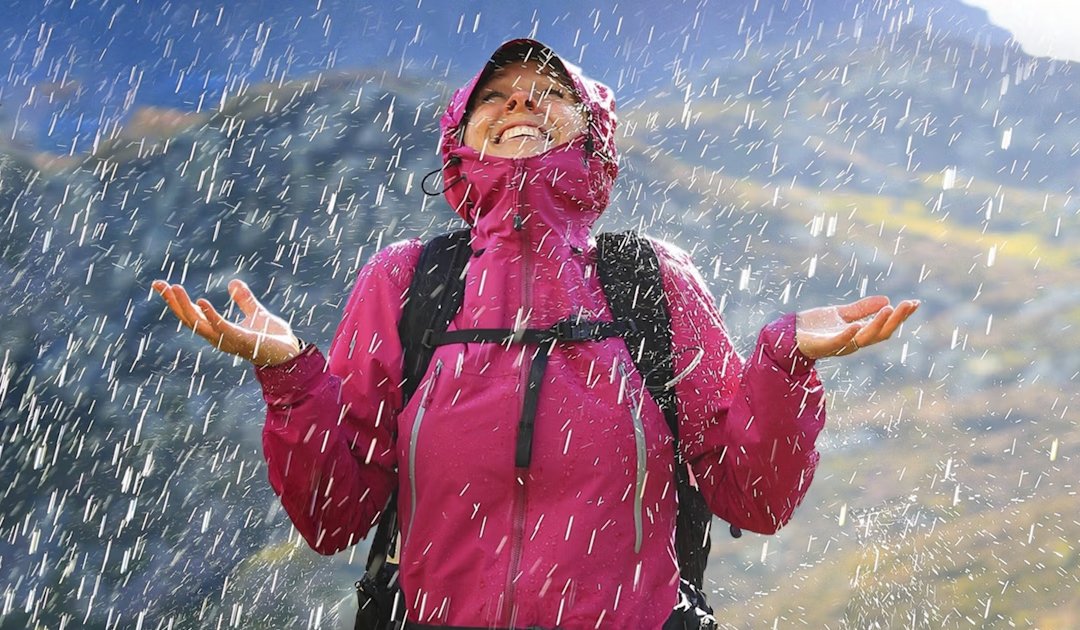
4. Determining the Heating System Voltage and Zones
Selecting the appropriate voltage and heating zones for the heating system is crucial for the garment’s heating performance and overall budget. Our extensive experience ensures we can recommend the optimal voltage and zone configurations to meet diverse customer needs.
- Voltage and Zone Options: Depending on the use case and heating requirements, we offer various voltage options ranging from 3.7V to 12V, and different heating zone configurations such as single-zone and multi-zone systems.
- Pros and Cons: Each voltage and zone configuration has its advantages and disadvantages. For example, 3.7V systems are more budget-friendly and consume less energy but provide less heat, making them suitable for lighter garments like gloves and socks. On the other hand, 12V systems offer superior heating performance and are ideal for extreme conditions, though they come with higher costs and energy consumption.
- Balancing Performance and Budget: Our expertise allows us to strike the right balance between performance and budget, ensuring that the heating system meets the specific needs of the customer without exceeding their financial constraints.
5. Selecting the Heating Material
Choosing the right heating material is vital for ensuring efficient and effective heat distribution. Our extensive research and development in this field allow us to provide the best solutions tailored to our customers’ needs.
- Material Options: Common heating materials include carbon fiber, composite filaments, alloy wires, and graphene.
- Performance Testing: Each material is tested for its thermal conductivity, durability, and flexibility to ensure it meets the product’s requirements.
6. Selecting the Battery
The battery is the power source for the heating system, and its selection is crucial for the overall performance and comfort of the garment. Leveraging our 11 years of experience, we guide our clients to choose the best battery options for their specific applications.
- Battery Types: Lithium-ion batteries are commonly used due to their high energy density and long lifespan.
- Size and Shape: The size and shape of the battery significantly affect the comfort and wearability of the garment. We carefully consider these factors to ensure the battery does not interfere with the user’s comfort.
- Capacity and Cost: The battery’s capacity determines the heating duration. Higher capacity batteries provide longer heating times but come at a higher cost. We work closely with our clients to balance the battery capacity and cost, taking into account the customer’s budget and the required usage duration to select the most suitable battery.
7. Creating Prototypes
Once the design and materials are finalized, the next step is to create prototypes. Prototyping is a critical phase where the initial design is turned into a tangible product.
- Sample Production: Using the selected materials and heating elements, prototypes are created according to the design specifications.
- Process Validation: This step verifies the manufacturing processes and ensures the prototype meets the design and functional requirements.

8. Testing the Prototypes
Testing is essential to ensure the prototype’s functionality, safety, and comfort.
- Functional Testing: Prototypes undergo rigorous testing to evaluate their heating performance, temperature control, and safety features.
- Scenario Simulation: The prototypes are tested in different environments and scenarios to ensure they perform well under various conditions.
- User Feedback: Collecting feedback from potential users helps identify any issues and areas for improvement.
9. Quality Control
Maintaining high-quality standards is crucial throughout the production process. Quality control ensures that each garment meets the company’s standards.
- Standards Development: Establishing detailed quality control standards covering raw materials, production processes, and final inspection.
- Multiple Inspections: Conducting multiple inspections throughout the production process to ensure consistent quality and safety.
10. Planning Mass Production
Once the prototypes are approved, the next step is to plan for mass production.
- Production Planning: Developing a production plan based on market demand and order quantities.
- Factory Preparation: Preparing the production line and necessary equipment to ensure smooth production.
- Process Monitoring: Continuously monitoring the production process to promptly address any issues and maintain product quality.
11. Final Product Inspection
Before the products are shipped, a final inspection is conducted to ensure they meet all quality standards.
- Final Inspection: Each product undergoes a thorough final inspection to check for any defects and ensure it meets the quality standards.
- Packaging and Storage: Approved products are packaged and stored properly, ready for shipment.
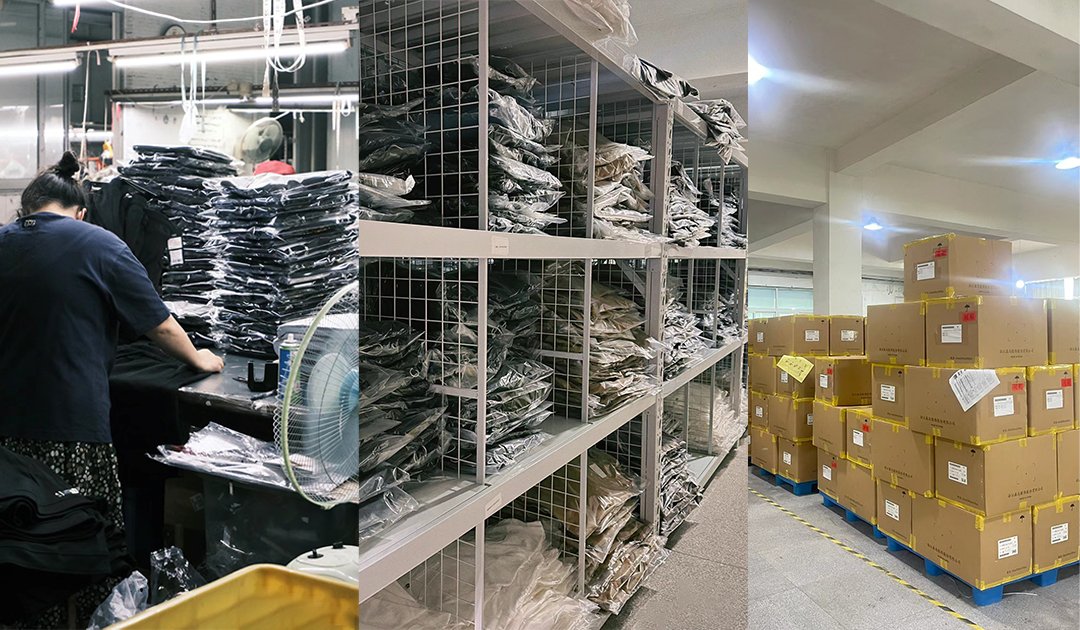
Conclusion
The production process of heated apparel is a complex and meticulous journey that starts with identifying the use case and ends with delivering the final product to the customer. Each step, from design to quality control, is crucial to ensure the final product is not only functional and safe but also stylish and comfortable. By understanding this process, customers can better appreciate the innovation and effort that goes into creating high-quality heated garments.
With over 11 years of experience in the industry, we pride ourselves on delivering tailored solutions that meet our clients’ specific needs. Our expertise and commitment to quality ensure that every garment we produce is of the highest standard, providing warmth, comfort, and style to our customers.